This case study focuses on how a major industrial client addressed frequent electric motor winding burnout by monitoring voltage irregularities with the Hioki PQ3198-94 Power Quality Analyser. By identifying and resolving voltage supply issues, the client successfully reduced motor downtime and maintenance costs.
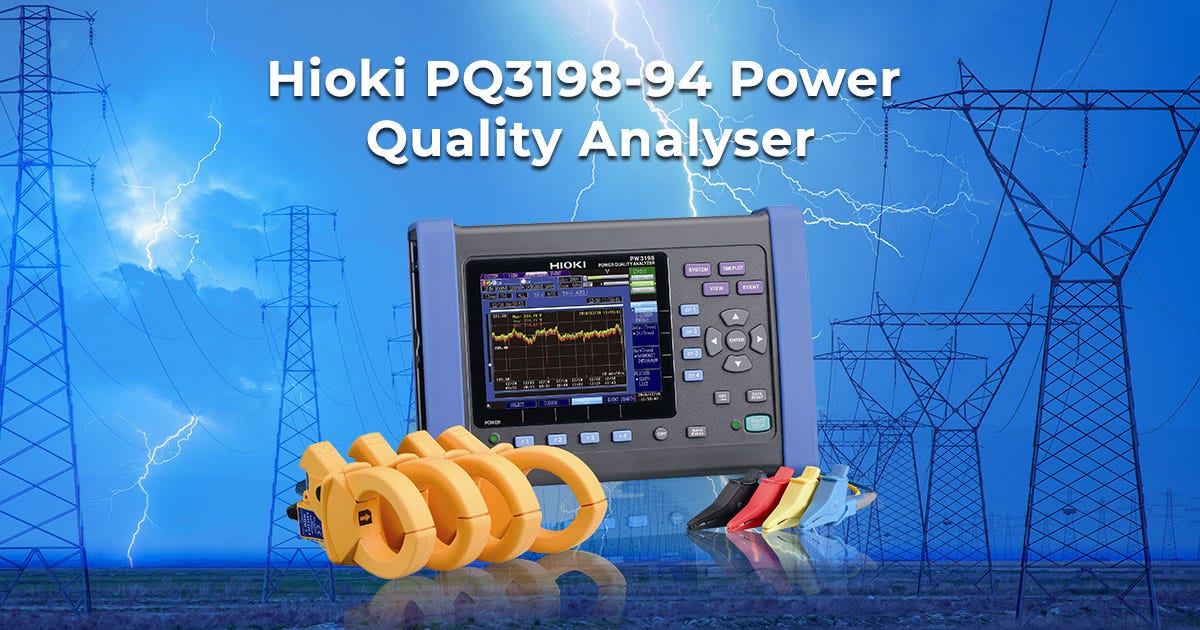
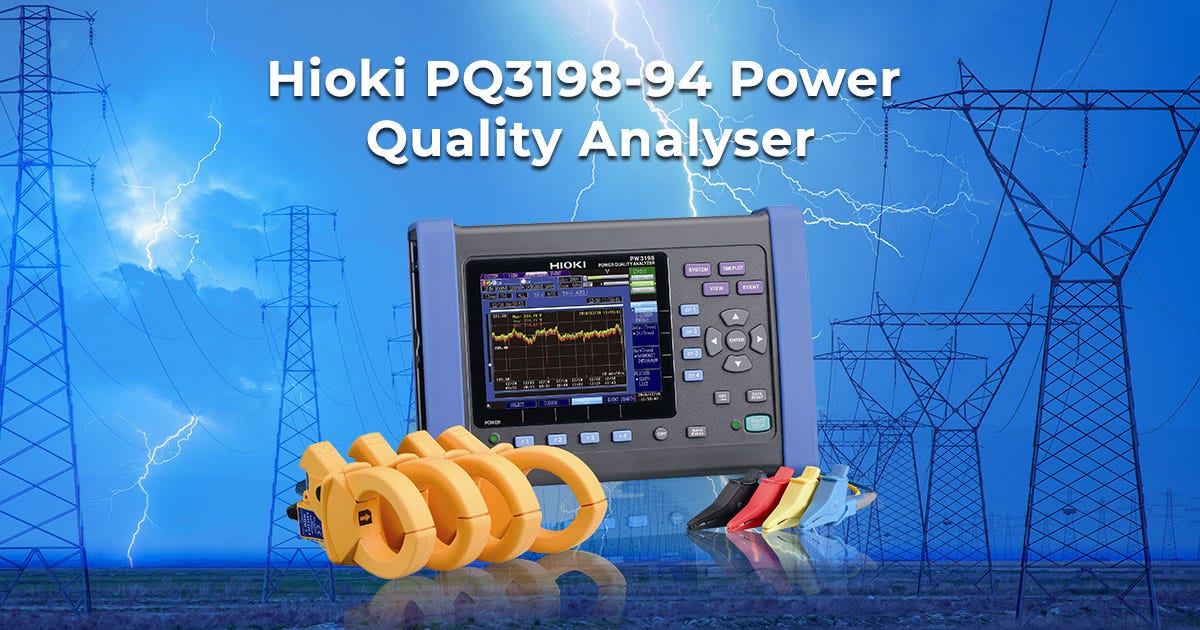
Challenge
Addressing Voltage Irregularities to Prevent Electric Motor Winding Burnout
A major industrial client, utilising large electric motors in their operations, experienced frequent issues with motor winding burnout. This recurring problem significantly disrupted their production process and incurred substantial repair costs. The issue was suspected to be caused by voltage irregularities in the power supply, which can stress the motor windings and lead to insulation degradation.
Solution
Utilising the Hioki PQ3198-94 to Identify Voltage Irregularities
The client opted to rent a Hioki PQ3198-94 Power Quality Analyser, which is designed to capture and log detailed data on various aspects of power supply quality. By using this unit, the client was able to monitor the voltage supply to the motor over several months. The analyser recorded key parameters, specifically looking for voltage spikes, dips, and other irregularities that could stress the motor windings.
Outcome
Proactive Power Monitoring
By using the Hioki PQ3198-94 Power Quality Analyser, the client was able to determine if the voltage supply was the cause of their motor burnout issue. This proactive approach allowed them to enhance the reliability of their electric motors, reduce downtime, and save on maintenance costs.